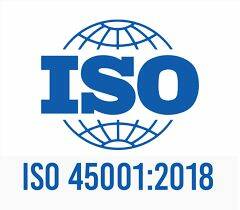
Fatal accidents
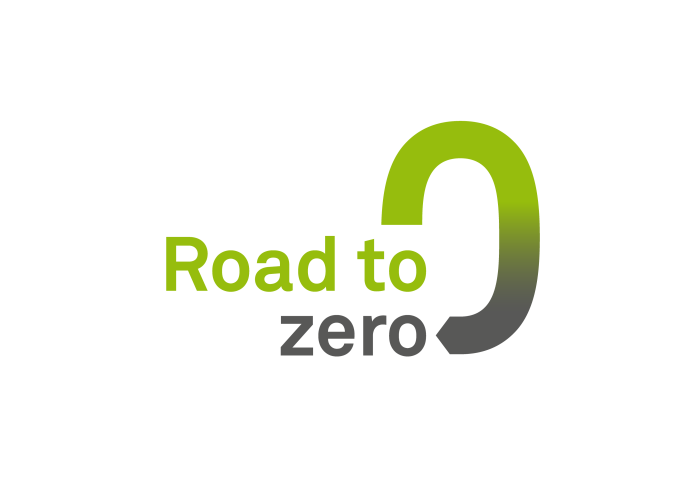
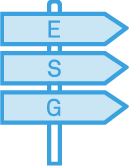
ESG roadmap to 2030
Goal: Maintain a safe working environment for all Stahl employees and contractors, with a goal of zero accidents
Severity rate of accidents
Topics addressed in this section:
> Health and safety
> Safety culture and KPIs
> Employee survey and training
> ISO 45001 certification
> Safety project in Bangladesh
Data verified and validated by Deloitte
Stahl’s ambition is to create a true safety culture, with a target of zero accidents and incidents. The Road to Zero (R20) program has been developed to support this goal. The program focuses on integrating safety into our company culture and ensuring all Stahl colleagues share the responsibility for safeguarding each other’s health and well-being. The key pillars of the program are:
A true safety culture is a mindset that prevails inside and outside the workplace;
A good safety record is never achieved through a large effort by a small group of people but by many small efforts from a large group of people;
The potential consequences of injuries at work mostly affect people and their social networks outside work; and
Stahl’s zero-tolerance policy on unsafe behavior ensures people are not injured at work.
Through R20, Stahl aims to increase employee engagement and safety awareness, so that safety is embedded in every level of our organization. In 2021, Stahl employees took part in the Organizational Cultural Diagnostic, a company-wide safety survey. The 97% response rate reflects the importance of this issue to employees. Key strengths and areas for improvement are summarized below.
LTI frequency rate
TRI = The total recorded injuries frequency rate is calculated as number of total recorded number of injuries in the last twelve months over total number of worked hours and referenced to a base of 1,000,000 h.
LTI = The lost-time injury frequency rate is the number of accidents involving the loss of one or more days of working time in the last twelve months over total number of worked hours and referenced to a base of 1,000,000 h.
The severity rate is the number of lost working days due to injuries in the last twelve months over total number of worked hours and referenced to a base of 1,000 h.
1.64
4.93
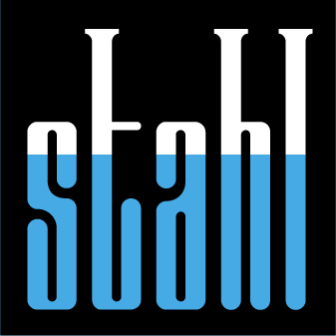
0.039
0.163
0
0
5.54

Back to overview
2022

Scroll
down
2021
2.33
-76%
TRI frequency rate
-67%
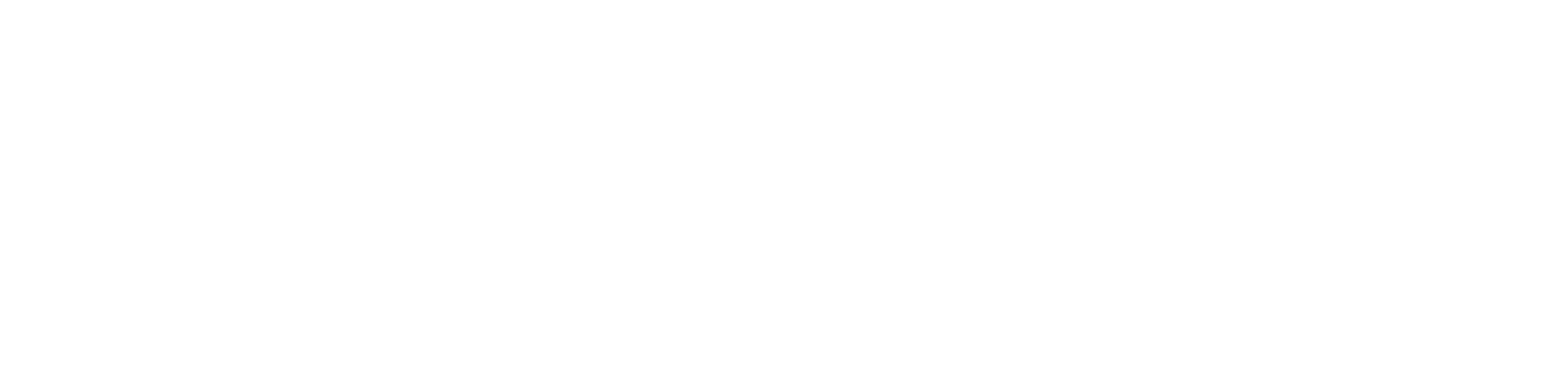
-58%
Ensuring the mental and physical well-being of all our stakeholders is an important foundation of Stahl's ESG approach. In this section, we explain how we ensure the safety of employees and contractors through training, policies, and certification; drive a culture of inclusion and diversity; and ensure fair and equitable labor practices throughout the supply chain.
Our safety vision
The occupational health and safety risks faced by Stahl employees include chemical contact and exposure to hazardous substances, chronic illnesses linked to chemical exposure, slips, trips, and falls, and serious incidents.
Watch our video interview with Alexis Pey, Global SHE Manager at Stahl, who explains our safety vision and the steps being taken to protect the health and well-being of Stahl colleagues at our sites round the world.
Key takeaways from the 2021 Organizational
Cultural Diagnostic survey
Safety-related communication: despite the good teamwork and family feeling, safety is not a common topic when communicating with colleagues.
The perception of safety as being fundamental and a top priority is not consistent at group level. Safety may be perceived as a responsibility that is not linked to some job positions.
Improvement
At all sites, people help and support each other, creating a “family-like” environment.
At local operational locations, employees are mindful of safety and are encouraged to report any (potential) safety issues.
Frontline employees have a good relationship with their supervisors and work very closely together.
At many sites, employees appreciate the efforts made by management to promote a safety culture and value the support they get from the company.
STRENGTH
Monitoring our safety results
Stahl reports on its safety KPIs, both internally and to shareholders, on a monthly basis. The reported metrics include injuries, incidents, audits, training, engineering projects, and preventative measures.
In 2022, the rate of accidents and injuries decreased significantly, resulting in a decline in the total recorded injuries (TRI) frequency rate, lost-time injury (LTI) frequency rate, and severity rate.
Improving on safety through policy and training
Stahl has dedicated policies in place to support our goal of zero injuries and accidents by 2030. Our health and safety policies apply to everyone who works at Stahl's locations, including temporary workers. Our broader focus on safety extends to our customers and the communities around our facilities.
Our Global Safety, Health & Environment Policy
Our Global Safety, Health, and Environment (SHE) policy focuses on building a strong company-wide safety culture, with an emphasis on implementing industry best practices and complying with legal requirements.
The key principles of our SHE policy are:
A strong safety culture involving the whole organization;
Safety, health, and environment as top priorities;
Prioritizing safety over short-term results;
Implementing industry best practices in addition to complying with all legal requirements; and
Knowledge as the basis of all decisions. Stahl will require employees to be trained in the skills necessary to carry out their duties and make decisions that help ensure safety.
Stahl’s Global SHE Manager is responsible for defining our SHE strategy, standards, and policies and implementing them throughout the company, and ensuring compliance. Our employees are regularly consulted on SHE policy developments and evaluations through local works councils.
Risk assessment
The Stahl Hazard Identification and Risk Assessment Methodology (SHIRAM) is our standard methodology for conducting safety risk assessments. This methodology has been designed to fit Stahl’s operations and processes and to integrate best practices for risk assessment and management. If our employees observe any additional hazardous conditions or behaviors, they are required to report them as part of our safety culture. When incidents occur, all Stahl sites are required to provide an investigation report. The methodology for this is defined at the local site level.
In 2021, Stahl implemented a new platform, the ARA Platform, based on SHIRAM, replacing the previous Stature Platform. We manage all studies through this platform, so we can easily share information between sites. In 2022, we took steps to strengthen the ARA Platform by introducing new templates and services and providing a clear reference within Stahl's digitalization landscape.
Training
We require all employees to be trained in appropriate safety skills, with the understanding that safety is a mindset, not a department, and that everyone at Stahl is responsible for ensuring it. Each Stahl site has a training matrix that defines the knowledge required to perform each job. Operators working in production, as well as colleagues in laboratories, logistics, Centers of Excellence, and offices, are trained according to their role and the risks involved.
Certification
We demonstrate our continuous safety improvements through ISO certification. As part of our ESG Roadmap to 2030, we have set a target to ensure all Stahl manufacturing sites are ISO 45001-certified. In 2022, 59% of our total production volume came from ISO 45001-certified sites. ISO 45001, which replaces the previous standard, OHSAS 18001, requires companies to take a more proactive approach to safety, assessing and addressing hazards and risks before they cause accidents or injuries. In contrast, OHSAS 18001 takes a reactive approach, focusing on risks rather than solutions. In line with this change, we have updated our approach to be more proactive.
Safety is also a key part of audits carried out by local authorities, with compliance necessary to receive certain permits.
Safeguarding the health and safety of our stakeholders
At Stahl, our responsibility for ensuring health and safety extends beyond our own workforce to our wider stakeholder base.
In 2022, we completed a long-running project in Bangladesh to help promote chemical safety in the local community. The project, run by TEGEWA, an association of chemical suppliers, of which Stahl is an active member, and the Dutch NGO Solidaridad, focuses on practical ways to improve the safety of chemical handling in the leather manufacturing cluster of Savar, in Dhaka, and to promote the well-being of factory workers in the cluster. As part of the initiative, Stahl helped to organize an intensive training campaign involving 1,200 workers, including 50 managers and 350 peer-trained workers. Several webinars were broadcast to raise further awareness of these issues. Following the successful completion of the project, Stahl will continue to support the Savar leather cluster on this critical issue as part of our overall commitment to sustainable development.
See the Environmental impact section of this report for information on how we ensure the health and safety of our value chain partners, including our approach to ensuring product safety for our customers and end-users.

Back
to top

Back to overview
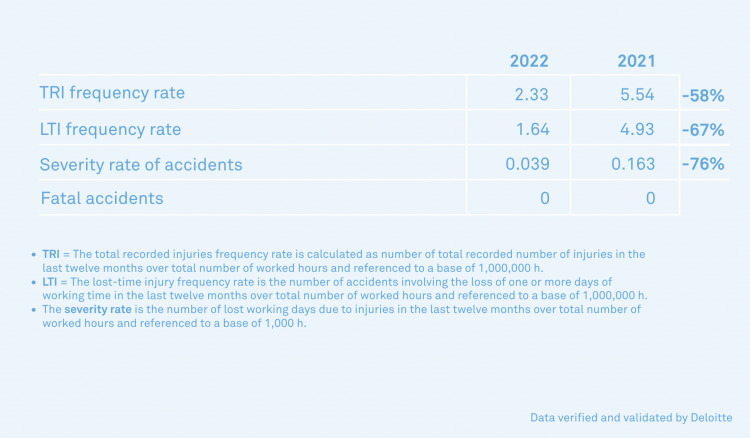
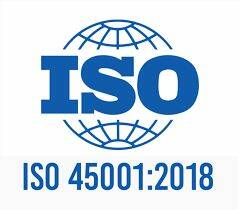

Back
to top
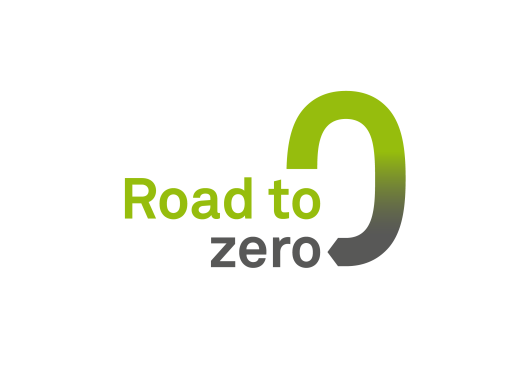
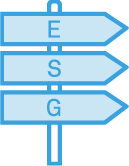
ESG roadmap to 2030
Goal: Maintain a safe working environment for all Stahl employees and contractors, with a goal of zero accidents
Stahl’s ambition is to create a true safety culture, with a target of zero accidents and incidents. The Road to Zero (R20) program has been developed to support this goal. The program focuses on integrating safety into our company culture and ensuring all Stahl colleagues share the responsibility for safeguarding each other’s health and well-being. The key pillars of the program are:
A true safety culture is a mindset that prevails inside and outside the workplace;
A good safety record is never achieved through a large effort by a small group of people but by many small efforts from a large group of people;
The potential consequences of injuries at work mostly affect people and their social networks outside work; and
Stahl’s zero-tolerance policy on unsafe behavior ensures people are not injured at work.
Through R20, Stahl aims to increase employee engagement and safety awareness, so that safety is embedded in every level of our organization. In 2021, Stahl employees took part in the Organizational Cultural Diagnostic, a company-wide safety survey. The 97% response rate reflects the importance of this issue to employees. Key strengths and areas for improvement are summarized below.
Safeguarding the health and safety of our stakeholders
At Stahl, our responsibility for ensuring health and safety extends beyond our own workforce to our wider stakeholder base.
In 2022, we completed a long-running project in Bangladesh to help promote chemical safety in the local community. The project, run by TEGEWA, an association of chemical suppliers, of which Stahl is an active member, and the Dutch NGO Solidaridad, focuses on practical ways to improve the safety of chemical handling in the leather manufacturing cluster of Savar, in Dhaka, and to promote the well-being of factory workers in the cluster. As part of the initiative, Stahl helped to organize an intensive training campaign involving 1,200 workers, including 50 managers and 350 peer-trained workers. Several webinars were broadcast to raise further awareness of these issues. Following the successful completion of the project, Stahl will continue to support the Savar leather cluster on this critical issue as part of our overall commitment to sustainable development.
See the Environmental impact section of this report for information on how we ensure the health and safety of our value chain partners, including our approach to ensuring product safety for our customers and end-users.
Certification
We demonstrate our continuous safety improvements through ISO certification. As part of our ESG Roadmap to 2030, we have set a target to ensure all Stahl manufacturing sites are ISO 45001-certified. In 2022, 59% of our total production volume came from ISO 45001-certified sites. ISO 45001, which replaces the previous standard, OHSAS 18001, requires companies to take a more proactive approach to safety, assessing and addressing hazards and risks before they cause accidents or injuries. In contrast, OHSAS 18001 takes a reactive approach, focusing on risks rather than solutions. In line with this change, we have updated our approach to be more proactive.
Safety is also a key part of audits carried out by local authorities, with compliance necessary to receive certain permits.
Training
We require all employees to be trained in appropriate safety skills, with the understanding that safety is a mindset, not a department, and that everyone at Stahl is responsible for ensuring it. Each Stahl site has a training matrix that defines the knowledge required to perform each job. Operators working in production, as well as colleagues in laboratories, logistics, Centers of Excellence, and offices, are trained according to their role and the risks involved.
Risk assessment
The Stahl Hazard Identification and Risk Assessment Methodology (SHIRAM) is our standard methodology for conducting safety risk assessments. This methodology has been designed to fit Stahl’s operations and processes and to integrate best practices for risk assessment and management. If our employees observe any additional hazardous conditions or behaviors, they are required to report them as part of our safety culture. When incidents occur, all Stahl sites are required to provide an investigation report. The methodology for this is defined at the local site level.
In 2021, Stahl implemented a new platform, the ARA Platform, based on SHIRAM, replacing the previous Stature Platform. We manage all studies through this platform, so we can easily share information between sites. In 2022, we took steps to strengthen the ARA Platform by introducing new templates and services and providing a clear reference within Stahl's digitalization landscape.
Our Global Safety, Health & Environment Policy
Our Global Safety, Health, and Environment (SHE) policy focuses on building a strong company-wide safety culture, with an emphasis on implementing industry best practices and complying with legal requirements.
The key principles of our SHE policy are:
A strong safety culture involving the whole organization;
Safety, health, and environment as top priorities;
Prioritizing safety over short-term results;
Implementing industry best practices in addition to complying with all legal requirements; and
Knowledge as the basis of all decisions. Stahl will require employees to be trained in the skills necessary to carry out their duties and make decisions that help ensure safety.
Stahl’s Global SHE Manager is responsible for defining our SHE strategy, standards, and policies and implementing them throughout the company, and ensuring compliance. Our employees are regularly consulted on SHE policy developments and evaluations through local works councils.
Improving on safety through policy and training
Stahl has dedicated policies in place to support our goal of zero injuries and accidents by 2030. Our health and safety policies apply to everyone who works at Stahl's locations, including temporary workers. Our broader focus on safety extends to our customers and the communities around our facilities.
Monitoring our safety results
Stahl reports on its safety KPIs, both internally and to shareholders, on a monthly basis. The reported metrics include injuries, incidents, audits, training, engineering projects, and preventative measures.
In 2022, the rate of accidents and injuries decreased significantly, resulting in a decline in the total recorded injuries (TRI) frequency rate, lost-time injury (LTI) frequency rate, and severity rate.
Key takeaways from the 2021 Organizational
Cultural Diagnostic survey
Safety-related communication: despite the good teamwork and family feeling, safety is not a common topic when communicating with colleagues.
The perception of safety as being fundamental and a top priority is not consistent at group level. Safety may be perceived as a responsibility that is not linked to some job positions.
Improvement
At all sites, people help and support each other, creating a “family-like” environment.
At local operational locations, employees are mindful of safety and are encouraged to report any (potential) safety issues.
Frontline employees have a good relationship with their supervisors and work very closely together.
At many sites, employees appreciate the efforts made by management to promote a safety culture and value the support they get from the company.
STRENGTH
Our safety vision
The occupational health and safety risks faced by Stahl employees include chemical contact and exposure to hazardous substances, chronic illnesses linked to chemical exposure, slips, trips, and falls, and serious incidents.
Watch our video interview with Alexis Pey, Global SHE Manager at Stahl, who explains our safety vision and the steps being taken to protect the health and well-being of Stahl colleagues at our sites round the world.
Ensuring the mental and physical well-being of all our stakeholders is an important foundation of Stahl's ESG approach. In this section, we explain how we ensure the safety of employees and contractors through training, policies, and certification; drive a culture of inclusion and diversity; and ensure fair and equitable labor practices throughout the supply chain.
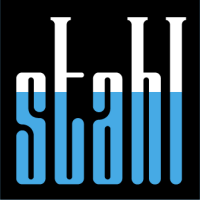